1.「しくみ・マネジメント」で重要な点の概要
◇企画決定の定義:最重要です
・企画決定時に決定すべき項目
Q:セールスポイント,Level Up VOC→開発目標,開発課題
C:売上目標,利益目標→売上台数,目標原価
D:開発スケジュール
・企画決定時に達成すべき状態
上記企画決定項目について実現できる目処がついている
●この部分を実現していないために多くのロスを発生している企業があります.
◇企画段階,開発段階での各部門の役割と責任の整合
貴社にとってどう開発したいかを考え,社内整合を取ります.
◇開発方針の整合
開発時に達成すべきStepはどの企業でも共通に考えることができます.
Step1:QCDの目標に対して達成できる目処がついた
Step2:市場品質を確保できる設計条件の決定
Step3:量産バラツキを確保できる公差の決定
*どのStepをどのDR(貴社の現状のしくみ)で実現するか=開発方針 です
●A社では企画決定時にStep2を達成する考えで進めています.
◇企画段階のしくみの強化
Planning Review 1:商品コンセプト,企画仮決定,開発課題の抽出と検討
Planning Review 2:マーケティングと企画修正,開発課題の検討
Planning Review 3:企画決定,開発課題の目処づけ完了
*上記Reviewをベースに,貴社ではどうするかを決めます.
◇開発段階のしくみの強化
・開発方針に基づいたしくみの強化を行います
・各部門の役割と責任の整合結果を盛り込みます
●何を実施したかのDRは意味がありません.
どういう状態を達成しているかをDRするのが重要です.
達成状態は上記Stepを意味します
2.「どうやって進めるか=人材育成」で重要な点の概要
◇市場品質確保・量産品質確保の考え方:下記は重要な点のみ
起因 |
分類 |
事前対策内容 |
有効な手法 |
設計起因 |
新技術 |
予測できない不良現象の事前対策 |
タグチメソッド,FMEA |
既存技術 |
過去不具合の再発防止 |
FTA,設計標準,ノウハウ,等 |
部品起因 |
新規部品 |
市場で大丈夫かどうかの認定評価 |
タグチメソッド |
既存部品 |
部品品質保証体制 |
(従来の品質保証の考え方) |
製造起因 |
新技術・工法等 |
予測できない不良現象の事前対策 |
タグチメソッド |
既存技術 |
量産品改善 |
QC工程表等の標準 |
*生産技術や検査設備設計は設計起因として考えてください.
●上記全てを実施しないと市場品質・量産品質は確保できません.
◇重点の決め方
1)QFDを活用して開発の重点=開発課題を決めます
開発課題=商品全体の課題(事業部全体の課題)
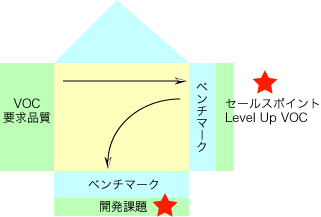
2)開発課題を技術課題,生産技術課題等に展開します.
技術課題,生産技術課題=開発対象システム の方がうまくいきます
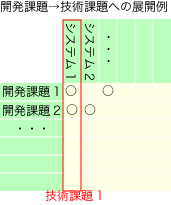
◇課題解決の重要な考え方
・評価:良いかどうかをデータを測定して調べる行為→設計を決める時に行う
<最も有効な手法> タグチメソッド
・試験:良いものができているのを確認する
・試作品:市場品質,量産品質が確保できているのを確認する「手段」
*良いかどうか分からないのに試作出図はしない |